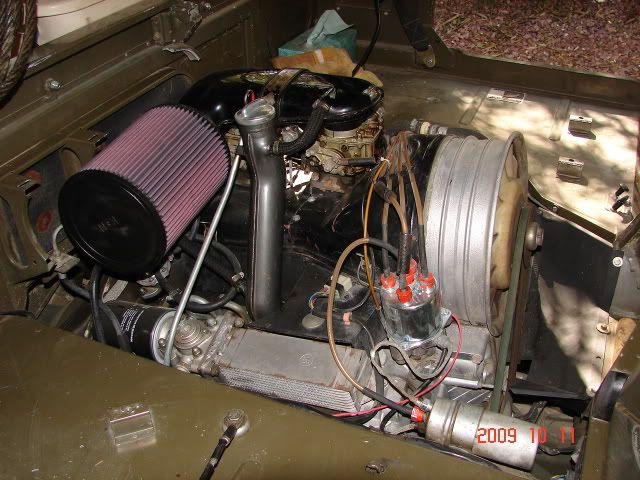
Here's the engine before the fun began, and I mean that literally because the Pinzgauer engine isn't really that difficult to work on. You can appreciate that it was designed to be serviced in the field when doing this kind of work. The solid core plug wires were made by Thilo in Prescott, AZ.
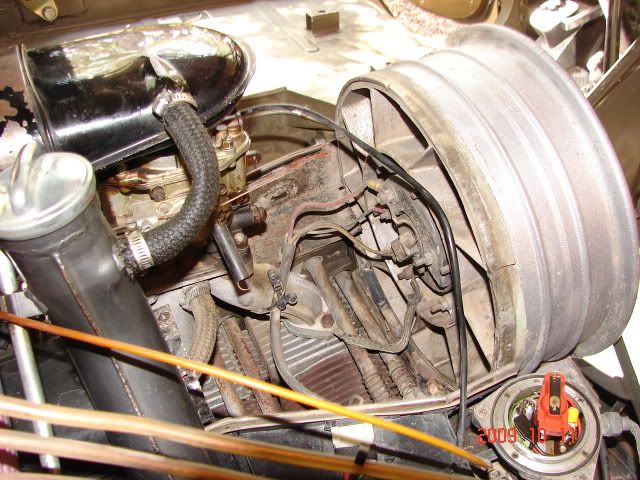
The plug wires and distributor cap removal make the forward sheet metal accessible.
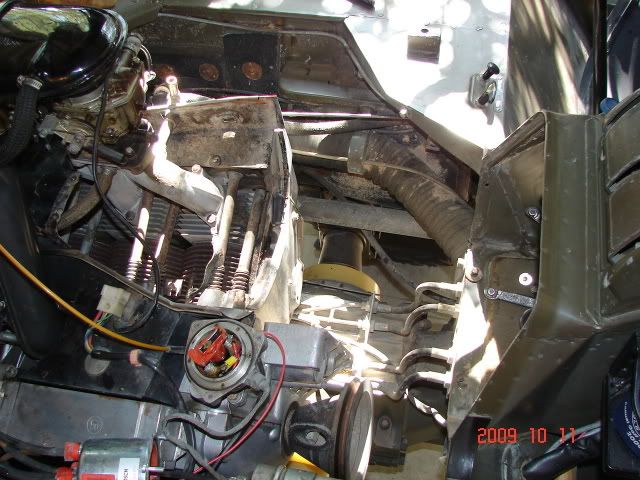
Once everything was out of the way I removed the entire fan housing as a unit with the alternator and fan still attached. Only 4 bolts hold it in place, all are easy to get at.
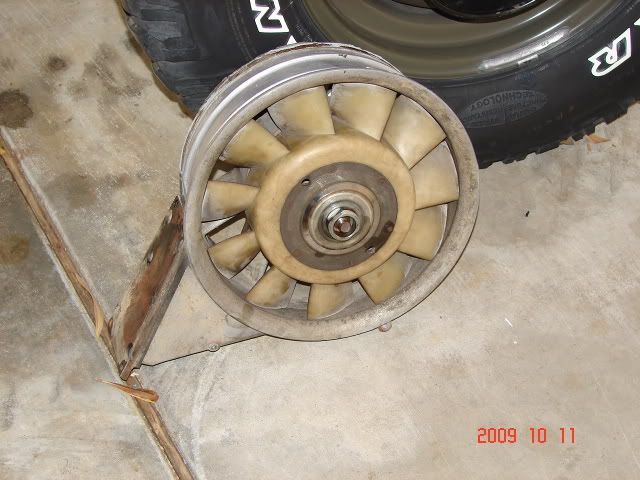
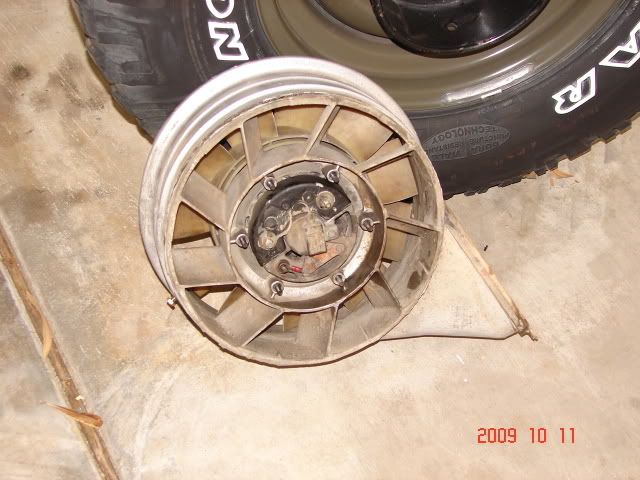
Here's the fan housing removed. I took it to the alternator shop just like this so they could have the fun of trying to remove the fan. After soaking the shaft for 2 days it came right apart.
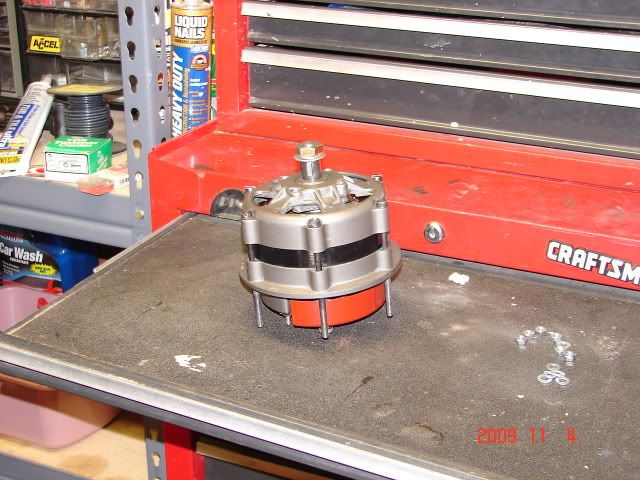
According to the shop, the rotor was failing- even though it was still charging OK. They had it rewound at a specialty shop in Washington state as a new part would have to be to be shipped in from Germany. The rest of the internal parts were replaced with factory parts I had on hand. As you can see, the shop returned the alternator looking and functioning like new.
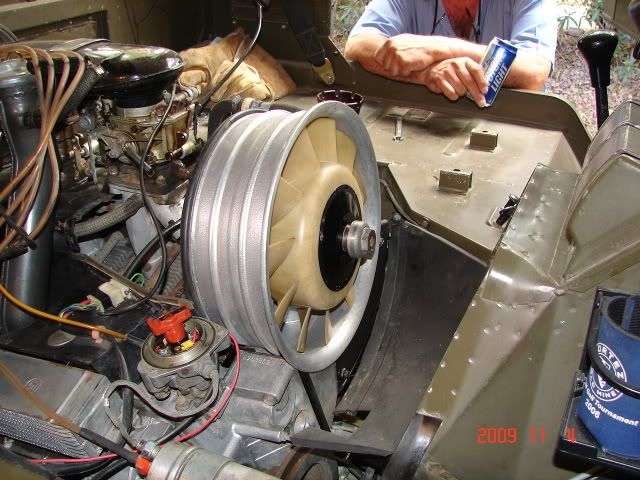
The fan housing back in place with a new seal, and all cleaned up. I replaced the alternator harness and cleaned the engine cylinders while it was apart. The red wire coming out of the distributor goes to the tach, and we all know how accurate that is.
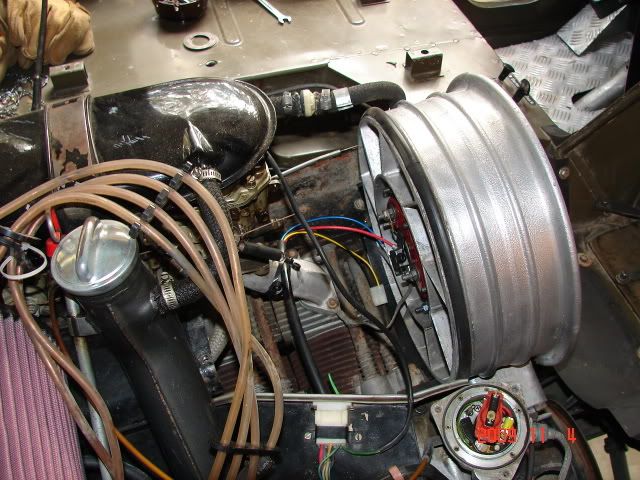
A last look before the cover is installed.
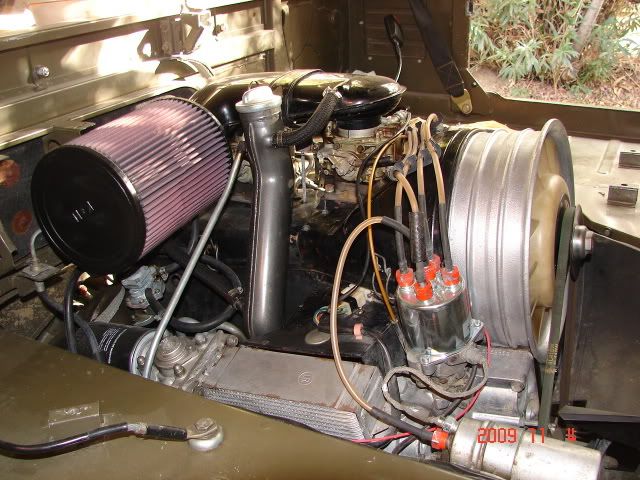
All back together and running, with the belt properly tensioned (3 shims in, 1 out). With all electrical devices operating simultaneously I registered less than 1/2 volt drop at idle. The voltage regulator was replaced, too.